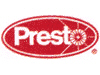
Presto GEOBLOCK® Porous Pavement SystemPP-Product Presentation For comprehensive information on the Geoblock®
Porous Pavement System, please click on the web site link listed above. Prestos Geoblock® Porous Pavement System is a series of interlocking,
polyethylene paving units designed to provide superior load support and turf protection
for emergency and utility access lanes, auxiliary parking, golf cart pathways,
trails, and other high-use application areas. The Geoblock® system
provides vehicular and pedestrian load support while protecting the grass from
the harmful effects of traffic. Working with the Environment
In many cities, current storm water management systems are pushed beyond their
capacities by run-off from traditional hard surfaces. With over 87% open area
at the surface, the Geoblock system offers a permeable solution. The Geoblock
design allows water to percolate into the ground through drain holes in the bottom
of the units, decreasing storm water run-off and allowing natural groundwater
replenishment. Under rainfall simulation of 64 mm/hour (2.5 inches), the run-off
coefficient for the Geoblock system is 1.5%. The Geoblock units are manufactured from up to 100% recycled polyethylene and
are inert to common chemicals, will not absorb moisture and are unaffected by
freeze-thaw cycles. ISO-Certified Quality
Presto’s commitment to quality begins with manufacturing and continues
through final installation. The quality management system for the sale, design
and manufacture of the Geoblock® system is certified to ISO 9001:2009 and
materials are specifically engineered in accordance with established geosynthetic
industry guidelines. The Geoblock® System Advantage - Fully Engineered System - Designed to provide long-term success; successful
installations since early 1980s.
- Permeable Design - 87% open surface; allows rain to percolate into the ground
rather than contribute to storm water runoff.
- Interlocking Unit Design - Maximizes load distribution capability.
- Protects the crown of the grass; prevents soil compaction when properly installed.
- Reduces the amount of site preparation and subgrade improvement.
- Easily Installed - Ordinary tools used to cut units does not require special
fasteners or connection devices.
A System with Integrity
The Geoblock system supports heavy or concentrated loads by creating a flexible
structural bridge within the topsoil layer that 1) maximizes load transfer from
block to block and 2) directly supports and distributes the concentrated loads
to prevent topsoil compaction and rutting. The system flexes under loads that
would break concrete.While some talk about strength per square foot, the structural integrity of
the Geoblock system is built in. The system features a four-sided tabular, interlocking
block design that provides superior load-bearing performance and performance and
layout design and construction flexibility. The recommended staggered placement
(bricklayers pattern) of the individual Geoblock units further increases the
systems load distribution capabilities and maximizes the number of adjacent units
used to effectively spread concentrated wheel loads over the largest possible
area.
UA-Uses, Applications
From fire access lanes to hiking trails, parking areas to golf cart paths, the
Geoblock system improves both the usefulness and aesthetics of an outdoor environment. - Emergency and utility access lanes
- Auxiliary parking areas
- Pedestrian walkways, trails and wheelchair access ways
- Approaches to monuments, statues and fountains
- Golf cart path shoulders and aprons
- Driveways, driveway shoulders and medians
Earn USGBC LEED™ credits for reducing site disturbance, storm water runoff
and heat island effects, and for recycled content. CP-Components, Parts
The Geoblock system is comprised of four major components:
1) The Geoblock unit, 2) the engineered base for support, 3) the selected topsoil
infill, and 4) the selected vegetation.Both the Geoblock unit and the base support soil work together to support the
imposed loading, while the Geoblock unit and the topsoil contribute to the vegetative
support. Other components may include a geosynthetic separation / reinforcement
layer, sub-drain components, and topsoil additives, which enhance vegetative
growth. Geoblock® Material Specification Material | Up to 100% recycled polyethylene | Color | Ranges from dark shades of gray to black. | Chemical Resistance | Superior | Carbon Black for Ultraviolet Light Stabilization | 1.5% - 2.0% | Unit Minimum Crush Strength @ 21°C (70°F) | 2,900 kPa (420 psi) | Material Flexural Modulus at 23°C (73°F) | 240,000 kPa (35,000 psi) | Nominal Dimensions (width x length) | 0.50 m x 1.00 m (1.64 ft x 3.28 ft) | Unit Depth | 50 mm (1.97 in) | Nominal Coverage Area | 0.50 m² (5.38 ft²) | Cells per Unit | 72 | Cell Size | 79 mm x 81 mm (3.1 in x 3.2 in) | Top Open Area per unit | 87% | Bottom Open Area per unit | 40% | Interlocking offset tabs | 1 tab for each per peripheral cell | Nominal Weight per Unit | 4.49 kg (9.9 lb) | Runoff Coefficient @ 63.5°mm/hr (2.5 in) Rainfall | 1.5% | Units per Pallet | 50 |
Note: Dimensions and weight are subject to manufacturing tolerances and
are influenced by recycled component characteristics.Geoblock® System Usage Guideline Load | Description | Depth of Engineered Base | 1 | Heavy Fire Truck Access & H-20 loading. Typical 620 kPa (90 psi) maximum
tire pressure. Single axle loadings of 145 kN (32 kip), tandem axle loadings of
220 kN (48 kip). Gross vehicle loads of 36.3 tonne (80,000 lb). Infrequent
passes. | 150 mm
(6 in) | 2 | Light Fire Truck Access & H-15 loading. Typical 586 kPa (85 psi)
maximum tire pressure. Single axle loadings of 110 kN (24 kip). Gross vehicle
loads of 27.2 tonne (60,000 lb). Infrequent passes. | 100 mm
(4 in) | 3 | Utility & Delivery Truck Access & H-10 loading. Typical 414 kPa (60
psi) maximum tire pressure. Single axle loadings of 75 kN (16 kip). Gross vehicle
loads of 18.1 tonne (40,000 lb). Infrequent passes. | 50 mm
(2 in) | 4 | Cars & Pick-up Truck Access. Typical 310 kPa (45 psi) maximum tire pressure.
Single axle loadings of 18 kN (4 kip). Gross vehicle loads of 3.6 tonne
(8,000 lb). Infrequent passes. | None | 5 | Trail Use: Loading for pedestrian, wheelchair, equestrian, bicycle, motorcycle
and ATV traffic. | None |
NOTE: The above applies when the natural ground has a California Bearing Ratio
(CBR) >= 3. As the CBR increases, depth of the engineered base will decrease.
Recommended Topsoil:
Suitable topsoil should be pulverized prior to filling the Geoblock cells and
contain sufficient organic content to support vegetative growth. Topsoil such
as sandy loam is recommended. Clay and clay loam materials are considered unacceptable. Recommended Engineered Base: Vegetated Systems
A recommended engineered base consisting of clear-stone / crushed rock having
an AASHTO #5 designation blended with topsoil will promote vegetative growth
and provide required structural support. The aggregate portion shall have particles
ranging in size from 9.5 to 25 mm (0.375 to 1.0 in) with a D50 of
13 mm (0.5 in). The percentage void-space when compacted shall be at least 30%.
Topsoil, equal to but not greater than the aggregate void percentage, shall
be added and blended prior to placement. The mixture shall be compacted to a
density that will provide a minimum California Bearing Ratio of 7%. Under some
conditions, a geotextile separation layer may be required between the natural
ground and the engineered base. AI-Assembly, Installation
The Geoblock system is designed for easy installation, requiring less site preparation,
less subgrade improvement, less excavation and less granular backfill than other
porous pavement systems. The Geoblock system installs easily around obstructions
and contours, and can be cut with ordinary hand or power tools. The four-sided
tabular, interlocking design saves installation time and money by eliminating
the need for special tools, staples, cleats and rings. The Geoblock systems
easy-to-handle size minimizes the quantity of blocks required on a given job,
reducing installation costs and labor. Installation Guidelines Subgrade Preparation
Excavate the area, allowing for the Geoblock unit thickness and the ‘engineered
base’ depth (where ‘engineered base’ is required). When
working with in-situ soils that have poor permeability, provide adequate
drainage from
the excavated area if the area has the potential to collect water. The in-situ
soil should be relatively dry and free from any standing water. Finish-grade
the surface of the in-situ soil specifically when the Geoblock unit is to
be
installed without an ‘engineered base’. Level and clear the area
of large objects such as rocks, pieces of wood, etc. to enable the Geoblock
units to interlock properly and remain stationary after installation. Geosynthetic Separation Layer
If required, the geosynthetic layer shall be rolled out over the prepared subgrade
along the alignment of the reinforced surface. The geosynthetic shall be pulled
taut to ensure that there are no folds. Geosynthetic layer overlaps, if required,
shall be according to plans. Sub-Drainage Component
If required, install the specified sub-drain and outlet according to construction
drawings. Ensure that a proper slope is maintained throughout the drainage system
and that the outlet is free from any obstructions preventing free drainage. Base Preparation
The strength of the porous pavement system is determined, in part, by the support
provided by a stable ‘engineered base’. Refer to the Geoblock
Usage Guideline for engineered base thickness recommendations. The health
of the vegetation,
however, requires that the ‘engineered base’ be loose to facilitate
root penetration. Start with an aggregate relatively free from fines and with
a void space of 30% or greater. The engineered base material is spread over the prepared base and compacted
to a density that will produce a CBR of 7%. Unit Installation Orientation & Laying Pattern of Units
Place the Geoblock units with the round hole to the ground. When the application
is an access lane, stagger the units to produce the bricklayer pattern. The
pattern is positioned such that the long direction of the unit is perpendicular
to the primary direction of traffic. When the application is a large area with
random traffic flow, stagger the units to produce the herringbone pattern. This
pattern reduces straight seams to one and a half block lengths. The staggered pattern is developed by using half Geoblock units made by field
cutting a full unit. Cut the units with a hand or power saw to custom fit both
contours and/or around obstructions. These final seam patterns assure maximum
load transfer and support. Other laying patterns are generally not recommended. Positioning of Units
Place the first row of Geoblock units against a stationary edge when available.
If the units are placed between two perpendicular or near-perpendicular stationary
edges (i.e. two parallel concrete curbs), allow for potential thermal expansion
of the Geoblock units by keeping the units away from the stationary edge. A compensation
of 1.375 in (34 mm) could be applied for each 10 ft (3 m) increment of length.
When the installation day(s) is optional, install the Geoblock units on cooler
cloudy days as opposed to hot sunny days. This will minimize the temperature gain
and resulting thermal expansion of the units when exposed to full sunlight for
several hours. Slide the units together so that the interlocking tab joint is fully engaged.
Units should be placed such that corners and seams do not protrude above the
desired surface elevation. The Geoblock units can be fixed in-place to prevent
the units from shifting during installation with optional wood or metal stakes,
or, by placing thread-forming tapping screws or nails through the perimeter
interlocking tabs. This may be needed if 1) trafficking / turning of heavier
construction vehicles causes movement of the units during the installation process
or 2) large temperature changes occur during the installation process.
Note that plastic has a relatively high rate of thermal expansion. Joint separation
and rejoining of separated units should be considered normal construction practice.
Once a healthy turf is developed, the root system will provide all necessary anchoring
of the system.
Unit Infilling
Infill the Geoblock units with the specified topsoil infill. Infilling should take place immediately after the units are installed to minimize the potential of joint separation caused by thermal expansion/contraction.
If the Geoblock units are to remain unfilled, contact Presto for recommendations.
Infill Procedures for Vegetated Systems
Infill the Geoblock units with a suitable topsoil. Use spreading methods that
will leave the cell infill uncompacted. Overfilling the cells is not recommended
since vehicular loading will cause undesirable compaction of the topsoil. For
application of the vegetation, see Finishing Procedures for Seeding and Sod Application.
Spread the infill material uniformly over the units to a level even with the
top of the cell wall.
Finishing Procedures
Seeding
Follow good seeding, fertilizing, and watering procedures for turf establishment
based on regional practices. An increase in watering frequency may be necessary
when free draining base materials are used. Use of a free draining base is generally
not recommended.
Sod Application
Sod can be used for areas where immediate use is desired. Young sod that is
free from netting materials is recommended. Mature sod with a more developed
root system and sod with netting may be difficult to press/cut into the Geoblock
cells.
When sod is used:
1) Sweep out the topsoil from the Geoblock unit to allow room to seat the sod.
Enough topsoil must be removed so that the crown of the sod is recessed slightly
below the top of the cell after pressing the sod in place. If too much topsoil
is removed, the bottom of the sod will not make contact with the topsoil after
it is pressed into the cell. Avoid removing too much topsoil.
2) Press the sod into the partially emptied cells using a roller or other suitable
equipment.
3) Use recommended watering procedures to ensure healthy sod growth.
Delineation
With vegetated systems, once healthy turf has been established, the Geoblock
cell wall structure will have minimal visibility when good turf-maintenance
practices are followed.
If used for an emergency access lane, delineation may
be desirable to create greater visibility. Delineation methods can include
the following: in-ground or above-ground curbing, shrubbery or vegetation,
perimeter
lighting or delineation markers, or other suitable systems.
Maintenance
If required, snow removal should be done using one of the following basic procedures:
- Keep a metal-edged plow blade a minimum of 25 mm (1.0 in) above the surface
during plowing operations, or
- Use a plow blade with a flexible rubber edge, or
- Use a plow blade with skids on the lower outside corners so that the plow
blade does not come in direct contact with the porous pavement system.
When deeper ground freeze occurs, the system functions as a typical hard pavement
surface. If a sharp metal plow-blade comes in direct contact with the surface
during plowing, any portion of the Geoblock system that protrudes above the
normal surface level could be removed by the blade.
TS-Technical Support
Presto Geosystems and its authorized distributors offer assistance in determining
the ideal Geoblock system for your specific application. In addition, the following
information is available for use by design professionals and contractors:
- Design Guidelines
- Material and CSI-Formatted Specifications
- CSI Format Specification
- Installation Guidelines
- Case Histories
- Technical Overview
- Test Documentation
MR-Manufacturer
Presto Products Company - Geosystems®
P.O. Box 2399
670 N. Perkins Street
Appleton, WI 54912-2399
Tel: (920) 738-1336
Toll-Free: (800) 548-3424
Fax: (920) 738-1222
Toll-Free Fax: (800) 535-8221
Web site: http://www.prestogeo.com
Email: info@prestogeo.com
PRESTO®, GEOSYSTEMS®, GEOWEB®,
ATRA® and SPECMaker® are registered trademarks
of Presto Products Company. LEED™ is a trademark of the US Green
Building Council. © 1998-2004
This information has been prepared for the benefit of customers interested in
the Geoweb cellular confinement system. It was reviewed carefully prior to publication.
Presto Products Company assumes no liability for its accuracy or completeness.
Final determination of the suitability of any information or material for the
use contemplated, or for its manner of use, is the sole responsibility of the
user.
|